Gas Filling Process
Please read these notes to select the most appropriate gas filling method for your production system.
How to gas fill IG units
IG units can be filled vertically or horizontally, through one hole or two holes in the spacer bar, or through gas filling corner keys. The holes can be drilled or punched. Inagas can supply a drill designed for the purpose to ensure accurate, consistent operation. See the Accessories page for more information.
Two hole filling is achieved either with gas filling corner keys or with gas filling sleeves inserted into the spacer bar. In either case, a gas barrier has to be made to prevent the gas from escaping during the filling procedure.
Hot melt sealant - vertical filling
Silicone plugs are inserted into the keys or sleeves and the sealant is continuously applied around the unit as normal. When the sealant has cooled, in 2-3 minutes, the silicone plugs are removed and the unit can be gas filled. Please note that the gas is always dispensed at the bottom of the unit, with the suction lance at the top. When using the single hole option this is placed at the top of the unit. For ensuring European EN1279 compliance the use of a primary seal or primary seal tape can be recommended to reduce gas loss to less than 1% per annum. See the PIB Tape page for more information.
The lances are inserted in the unit as shown.
The equipment gives an audible signal when the unit has the correct level of gas. The top lance is removed first and the gas plug inserted; this procedure is repeated for the lower hole. The sealant void behind the plug can be conveniently sealed using a portable hot melt gun or by using the bulk hot melt applicator. See the Portable Hot Melt Guns page for more information.
Two part sealant - vertical filling
Two part sealant should be used in conjunction with a butyl primary seal. The butyl can provide an excellent gas barrier if applied properly, however, a problem can arise when used with cut spacer bar. The gas may leak through the ends of the bar unless they are sealed with the butyl.
Provided the butyled spacer frame can give a good gas barrier, the procedures are as above, but omitting the use of the silicone plug - the secondary sealant being applied after the gas filling cycle. If a butyl gas barrier cannot be established, the procedures for the hot melt system may be used. The use of pre-bent spacer bar will prevent any problems with gas leakage provided the butyl primary seal is properly applied.
Super Spacer
Either two holes or one hole filling can be achieved using the Super Spacer as the gas barrier, however on large toughened glass units it may be advisable to use the hot melt edge sealant as the gas barrier leaving spaces for the gas filling holes.
Smartfill
The Smartfill range of gas fillers can also be used in one hole filling configuration.
The procedures are similar to those above, but using a single lance which dispenses gas and removes air simultaneously. This system is convenient as there is only one hole to prepare and the unit may be filled either vertically or horizontally. Typically, one hole filling is slower than two hole filling, however, in terms of production flow, this time difference is offset by the reduced frame preparation. Please note that larger units should be filled vertically to maintain equalisation.
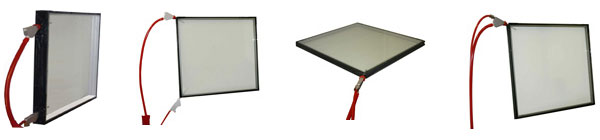